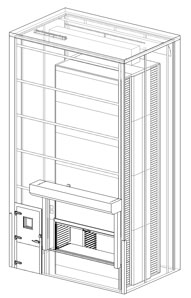
Abstract
The refrigerated Hänel Lean-Lift® Vertical Lift Module (VLM) is a cutting-edge storage solution that provides efficient and organized storage while maintaining temperature control for sensitive materials. This white paper outlines the challenges faced during the development and installation of the refrigerated Hänel Lean-Lift® VLM system in a pharmaceutical plant in the US. It discusses the creative solutions devised to overcome these challenges, ensuring the redundancy of the refrigeration system, installation sequence, efficient air circulation, maintaining the temperature uniformity in the space, and reliable system operation.Keywords: Controlled Environmental Rooms, High Density Storage, Temperature Mapping
Introduction
The refrigerated (+5°C ±3°C) Hänel Lean-Lift® VLM is a revolutionary storage system that integrates temperature control capabilities into the space-saving vertical storage solution. This white paper delves into the key challenges encountered during the project, emphasizing the technical and logistical complexities that needed to be addressed.Challenges and Solutions
Next few paragraphs describe the challenges and implemented solutions.1. Refrigeration System Redundancy and Space Limitation
The project required two independent refrigeration systems to minimize the downtime. However due to space constraints, placing two evaporator units in the room was not feasible. Labworks has come up with a creative solution to ensure redundancy and maintain temperature consistency. The solution involved employing a face-split coil configuration within a single evaporator casing, maximizing space utilization while ensuring reliable temperature control even in the event of a coil failure.2. Installation Sequence
Installing the refrigerated Hänel Lean-Lift® in a confined space required careful consideration of the installation sequence. The optimal sequence involved constructing three walls, installing the evaporator unit, positioning the Lean-Lift® storage system, and then completing the installation with the front wall. This sequence allowed for efficient utilization of space and minimized disruptions during installation. Front wall installation presented challenges due to batten strips (FM 4880 requirement) that required precise placement to ensure a secure fit. The solution involved meticulous pre-planning and alignment procedures, ensuring that the batten strips were seamlessly integrated to provide structural integrity and meet the requirements.3. Air Circulation Within the Space:
Efficient air circulation was crucial to maintain uniform temperature distribution. The evaporator unit cooler was installed 26.5ft above floor, and in order to address the challenge of minimizing pressure drop and ensuring warm air's return to the evaporator, deflectors were strategically placed to guide airflow. This solution not only maintained temperature uniformity but also enhanced energy efficiency. Figure 1 illustrates the effect of axial fans.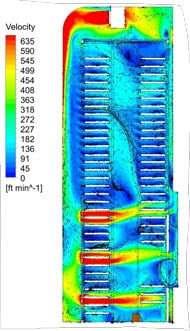
4. Maintaining Temperature Uniformity Through Hänel Lean-Lift®:
The solid shell design of the Hänel Lean-Lift® posed a challenge for air circulation. Computational Fluid Dynamics (CFD) simulations were employed to identify potential circulation issues and areas that need improvement. Subsequently, axial fans were strategically integrated to improve airflow within the system, ensuring consistent temperature control across all stored items. Figure 2 and 3 respectively depict the CFD result as well as the temperature mapping result, which stunningly all 25 probes are within ± 1°F.Table 1 shows the min and max temperature during 24 hours temperature mapping.
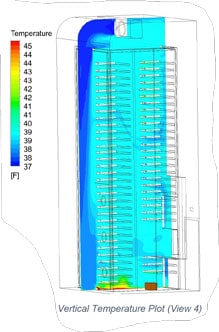
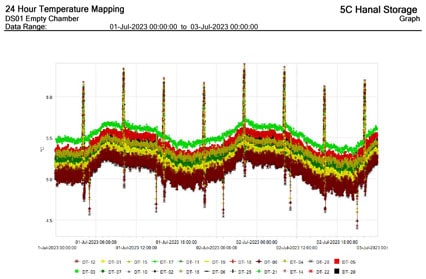
5. Roll-Up Door Heights:
To facilitate both operation and maintenance, the roll-up door was designed to stop at two different heights. This solution allowed convenient access during routine operation and comprehensive access for maintenance and repair activities, enhancing the system's user-friendliness and overall reliability.6. Dual Redundancy on PLC:
Ensuring the system's uninterrupted operation was paramount. To achieve this, a dual redundancy approach was implemented for the Programmable Logic Controller (PLC) and all input/output (I/O) cards. This redundancy ensured that in case of a failure, the backup PLC seamlessly takes over, minimizing downtime and maximizing system reliability.Conclusion
The refrigerated Hänel Lean-Lift® project posed several intricate challenges, from optimizing coil configurations to ensuring efficient air circulation and maintaining system redundancy. Through creative solutions such as face-split coils, deflectors, axial fans, and running CFD calculation during the engineering phase, these challenges were successfully overcome, resulting in a highly efficient and reliable temperature-controlled storage solution. The successful implementation of these solutions showcases the importance of comprehensive planning, strategic problem-solving, and collaboration in tackling complex engineering projects.Future Considerations
As technology continues to advance, future iterations of the refrigerated Hänel Lean-Lift® could incorporate predictive maintenance features, improved energy efficiency, and further automation to enhance the user experience and meet evolving industry standards.References
TablesTable 1 (Min and Max values in 24 hours temperature mapping)
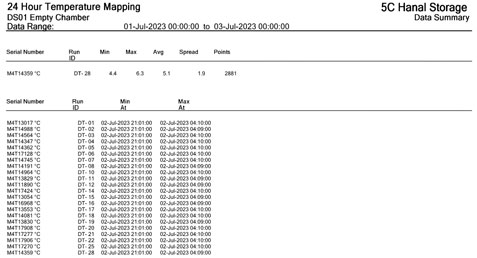
About Hänel Storage Systems
Founded in Germany in 1953, Hänel’s North American headquarters has been located in Pittsburgh, PA since it was established in 1984. Hänel Storage Systems specializes in the design and engineering of Rotomat® vertical storage carousels and Lean-Lift® Vertical Lift Modules for a wide range of industries and applications. Hänel provides sales, service and technical support to North and South America through a network of factory-trained channel partners and service providers. Introduced in 1957, the Rotomat® Vertical Carousel is based on the Ferris Wheel principal. Inventory is stored in a series of carriers that rotate within an enclosed unit and are accessed at a single opening. This vertical “goods to the user” concept improves productivity, lowers costs, increases security and saves valuable floor space. Introduced in 1994, the Lean-Lift® Vertical Lift Module stores inventory on trays that are automatically measured for height each time they enter the unit. A vertical extractor places each tray within the unit in a location that maximizes available storage space. Trays can be equipped with dividers, totes, bins and specialized holders to store any type of inventory.
Leave A Comment